KONČAR - Electrical Engineering Institute
We research, develop, test and certify. We leverage cutting-edge technologies to discover innovative solutions for efficient power conversion and transmission.
Izbornik na naslovnici
Innovation and responsibility in Science
For more than six decades, we have been participating in the development of new and innovative products and services in the fields of transformers, rotating machines, high-voltage and medium-voltage equipment, power converters, and railway vehicle components. We are a globally recognized partner that contributes to the success of KONČAR.
We conduct testing of electrical equipment and mechanical components in our own Laboratory Center, with more than 750 accredited testing and calibration methods across 9 modernly equipped laboratories. Our product conformity assessment service operates in accordance with international, European, and Croatian standards.
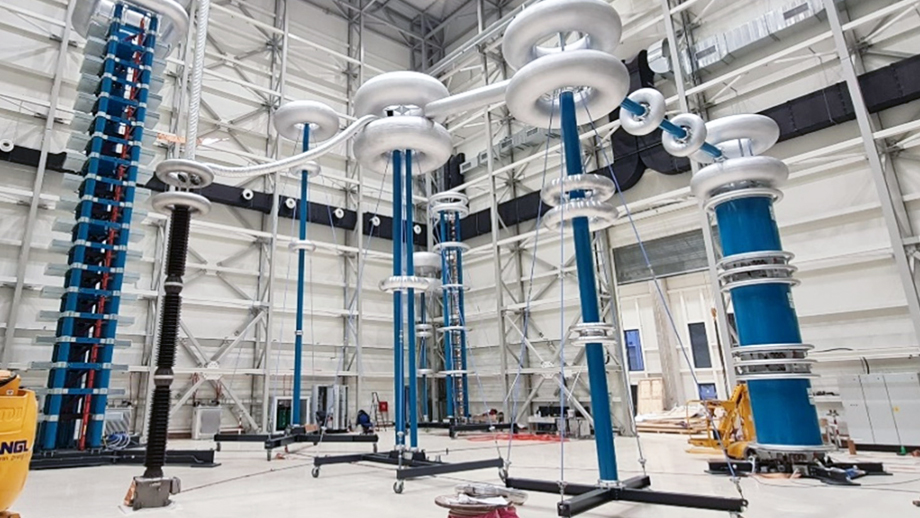
Laboratory Center
Our Laboratory Center offers a comprehensive range of services including testing, calibration, and certification to ensure product compliance with relevant standards and directives.
We also perform diagnostic testing on equipment used in power facilities and provide technical supervision during construction, showcasing the broad scope of our expertise.
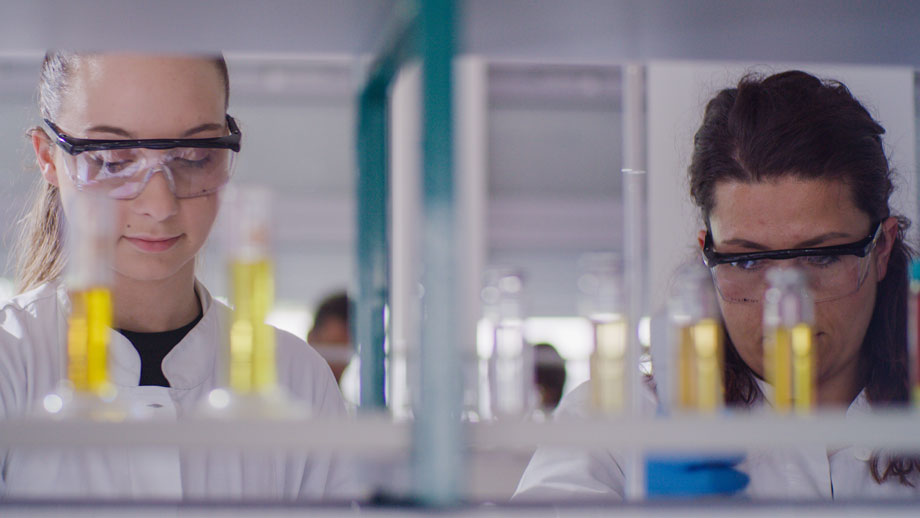
Research and Development
Our groundbreaking scientific research has made notable strides in areas such as transformers, rotating machinery, high-voltage equipment, energy converters, and rail vehicle components. These advancements have led to the creation of high-tech solutions leveraging state-of-the-art information and communication technologies, including power equipment monitoring systems, control systems, and embedded computer systems.
News & stories
Find out more about the recent activities, successes and flagship projects.
Flagship projects
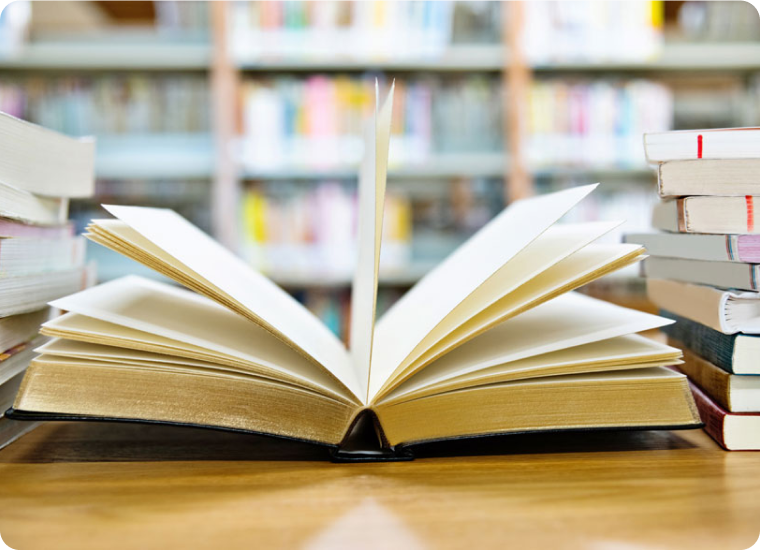
Information and Documentation Department and Library
The department has a long and rich tradition dating back to 1946, when the library of the then company Rade Končar was established. Today, we are here to share resources with the local and international community and provide access to information. We support high-quality research and development and are responsible for preserving and protecting professional knowledge.
We manage a collection of over 20,000 printed professional books and more than 800 titles of scientific and professional journals in the fields of electrical engineering, electronics, energy, and transportation.
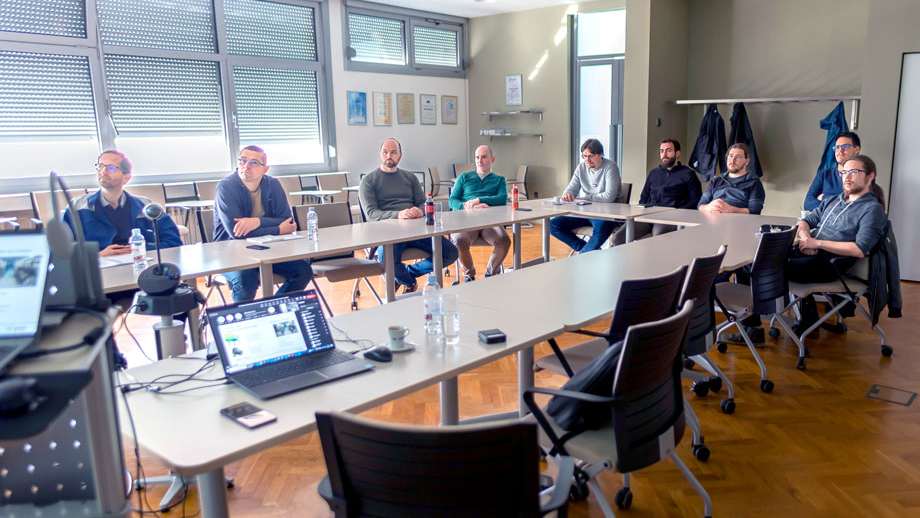
Digital Factory Lab
KONČAR Digital Factory Lab is a virtual hub built around high-tech software solutions for the manufacturing industry. The concept of this innovation lab is to make the journey towards digital transformation, digital factories, and Industry 4.0 more accessible and less risky.
DFL is an initiative led by KONČAR, Dassault Systèmes, and CADCAM Group. Other partners are welcome to join the initiative permanently or temporarily if it aligns with the interests of the project. Companies, consultants, institutions, universities, or individuals can join the project, and each stakeholder may have different reasons for participation in the innovation lab. The greatest opportunities the Lab offers are development of strong business and technological relationships, exploration of new technologies, transfer of knowledge and improved market visibility.
Get in touch
At KONČAR, we continuously create new opportunities for individuals with diverse skills and educational backgrounds.
We’re always excited to meet new talent
Explore all jobs and open positions, find the right fit for you or send us an open application.
Your reliable partner in the fields of power engineering, rail vehicles, and railway infrastructure, laboratory testing, diagnostics, and certification.
If you have any questions about our products, contact our team. We are here to help you find the perfect solution for your business! info@koncar-institut.hr
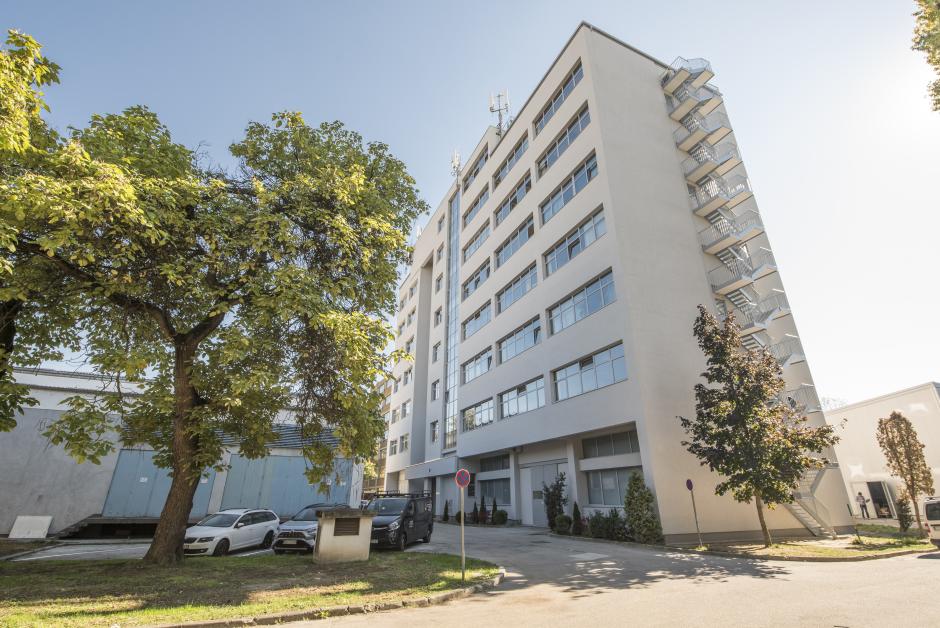
Company name: KONČAR – Electrical Engineering Institute Ltd. for research, development, and services
Company's abbreviated name: KONČAR – Electrical Engineering Institute Ltd.
Address: Fallerovo šetalište 22, HR-10000 Zagreb, Croatia
Managing Board: Dalibor Filipović-Grčić, Ph.D., Director
Phone: + 385 (0) 1 3667 315
E-mail: info@koncar-institut.hr
Registration court: Zagreb Commercial Court
Court Registered Number: 080143769
VAT ID No.: HR37724368086
Equity capital: 5.410.000,00 EUR paid in full
Commercial bank: Zagrebačka banka d.d., Zagreb
IBAN: HR6923600001101228876
General terms and conditions of sales
General terms and conditions of purchase
Special terms and conditions of sales for testing and certification services